FPSO & Vessels
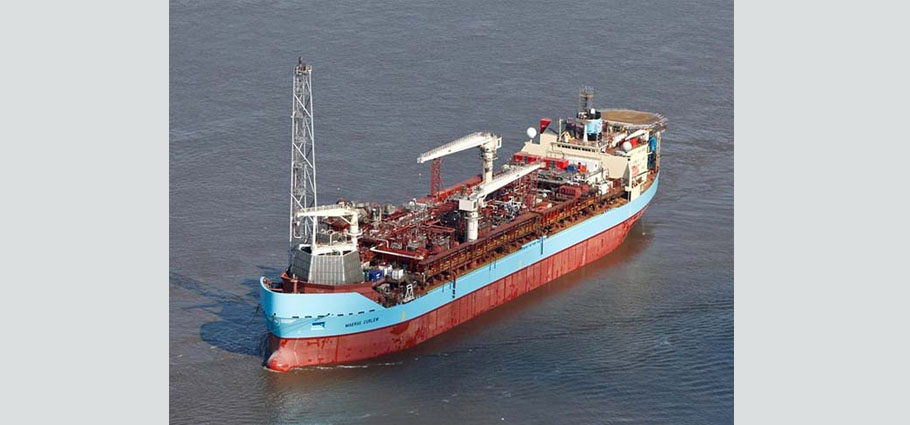
Monitor Systems Engineering have nearly two decades of experience in the design and manufacture of safety, critical, operational instrumentation and monitoring systems for all offshore rigs including support vessels and FPSO's, Floating Production Storage and Offloading Vessels.
Experience: over the years, Monitor Systems has built a significant reputation providing high quality bespoke and regular engineering solutions for safe and hazardous working areas in the offshore oil and gas industry. Our experience and proven capability in the design and manufacture of instrumentation and monitoring systems is well know throughout the oil and gas industry.
FPSO's, Floating Production Storage and Offloading Vessels are very similar in nature to other offshore vessels like jack-up rigs, semi-submersible rigs and drilling platforms, and they share a similar type of equipment and instrumentation for day to day operations. Monitor Systems have extensive experience working on all of these offshore oil and gas vessels including FPSO's, from detailed equipment survey to the design, manufacture and installation of instrumentation and monitoring systems.
General: A floating production, storage and offloading FPSO unit is a floating vessel used by the offshore oil and gas industry for the processing of hydrocarbons and for storage of oil. An FPSO vessel is designed to receive hydrocarbons produced from nearby platforms or subsea template, process them, and store oil until it can be offloaded onto a tanker or, less frequently, transported through a pipeline. FPSO's Floating Production Storage and Offloading Vessels are preferred in frontier offshore regions as they are easy to install, and do not require a local pipeline infrastructure to export oil.
Oil produced from offshore production platforms can be transported to the mainland either by pipeline or by tanker. When a tanker is chosen to transport the oil, it is necessary to accumulate oil in some form of storage tank such that the oil tanker is not continuously occupied during oil production, and is only needed once sufficient oil has been produced to fill the tanker.
Floating production, storage and offloading vessels are particularly effective in remote or deepwater locations where seabed pipelines are not cost effective. FPSOs eliminate the need to lay expensive long-distance pipelines from the processing facility to an onshore terminal. This can provide an economically attractive solution for smaller oil fields which can be exhausted in a few years and do not justify the expense of installing a pipeline. Furthermore, once the field is depleted, the FPSO can be moved to a new location.
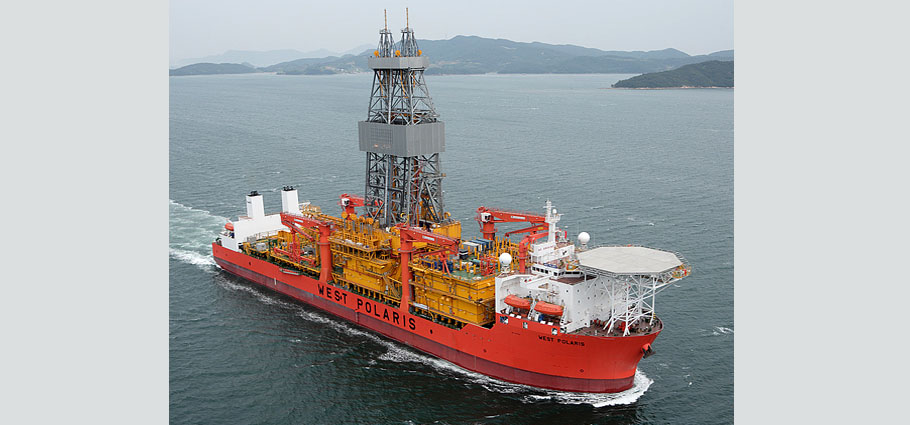
Monitor Systems Engineering specialise in the design and manufacture of safety, critical, operational instrumentation and monitoring systems for Drillships.
Drillships, like jack-up rigs, semi-submersible rigs and drilling platforms share a similar type of equipment and instrumentation for day to day operations. Monitor Systems have extensive experience working on all of these offshore oil and gas vessels, from detailed equipment survey to the design, manufacture and installation of instrumentation and monitoring systems.
History and General: A drillship is a merchant vessel designed for use in exploratory offshore drilling of new oil and gas wells or for scientific drilling purposes. In most recent years drillships are used in deepwater and ultra-deepwater applications, equipped with the latest and most advanced dynamic positioning systems.
The drillship can be used as a platform to carry out well maintenance or completion work such as casing and tubing installation, subsea tree installations and well capping. Drillships are often built to the design specification to meet the requirements set by the oil production company and/or investors.
In 2013 the worldwide fleet of drillships tops 80 ships, more than double its size in 2009. Drillships are not only growing in size but also in capability with new technology assisting operations from academic research to ice-breaker class drilling vessels. U.S.
Drillships are just one way to perform various types of drilling. This function can also be performed by semi-submersibles, jackups, barges or drilling platform rigs.
Unique Features: Drillships have the functional ability of semi-submersible drilling rigs and also have a few unique features that separate them. First being the ship-shaped design. A drillship has greater mobility and can move quickly under its own propulsion from drill site to drill site in contrast to semi-submersibles and jackup barges and platforms. Drillships have the ability to save time sailing between oilfields worldwide. A drillship takes about 20 days to move from the Gulf of Mexico to the Offshore Angola. Whereas, a semi-submersible drilling unit must be towed and takes about 70 days, more than three times as long.
Drillship construction cost is much higher than that of a semi-submersible. But although mobility comes at a high price, the drillship owners can charge higher day rates and get the benefit of lower idle times between assignments.
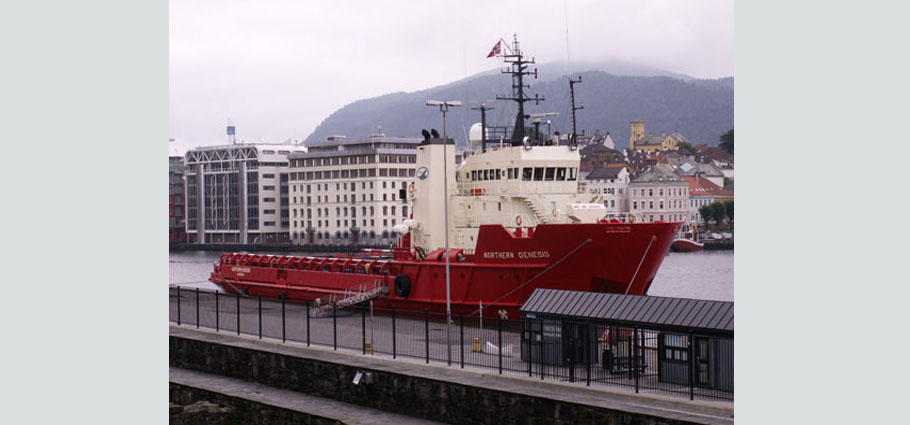
Monitor Systems specialise in the design and manufacture of safety, critical, operational instrumentation and monitoring systems for offshore platform supply and support vessels.
Monitor Systems have experience working on supply/support vessels; undertaking detailed equipment survey, design, manufacture and installation of monitoring and instrumentation systems.
General: A platform supply/support vessel is a ship specially designed to supply and support offshore oil platforms. These supply/support vessels range from 20 to 100 meters in length and accomplish a variety of tasks, and need specialised instrumentation and equipment to do so. The primary function for most of these supply/support vessels is transportation of goods and personnel to and from offshore oil platforms and other offshore structures.
In recent years a new type of platform supply/support vessels entered the market, usually equipped with a Class 1 or Class 2 Dynamic Positioning System.
Supply and Support: Cargo tanks for drilling mud, cement, diesel fuel, potable and non-potable water, and chemicals used in the drilling process comprise the bulk of the cargo spaces. Fuel, water, and chemicals are almost always required by oil platforms. Certain other chemicals must be returned to shore for proper recycling or disposal.
Equipped: Common and specialty tools are carried on the large decks of these platform supply/support vessels. Most carry a combination of deck cargoes and bulk cargo in tanks below deck. Many ships are constructed (or re-fitted) to accomplish a particular job. Some of these platform supply/support vessels are equipped with a firefighting capability and fire monitors for fighting platform fires. Some vessels are equipped with oil containment and recovery equipment to assist in the cleanup of a spill at sea. Other platform supply/support vessels are equipped with tools, chemicals and personnel to "work-over" existing oil wells for the purpose of increasing the wells' production.
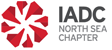







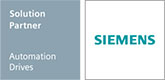

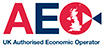

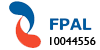